Human-Machine Collaboration: How Palletizers and Workers Improve Efficiency
2025-06-07
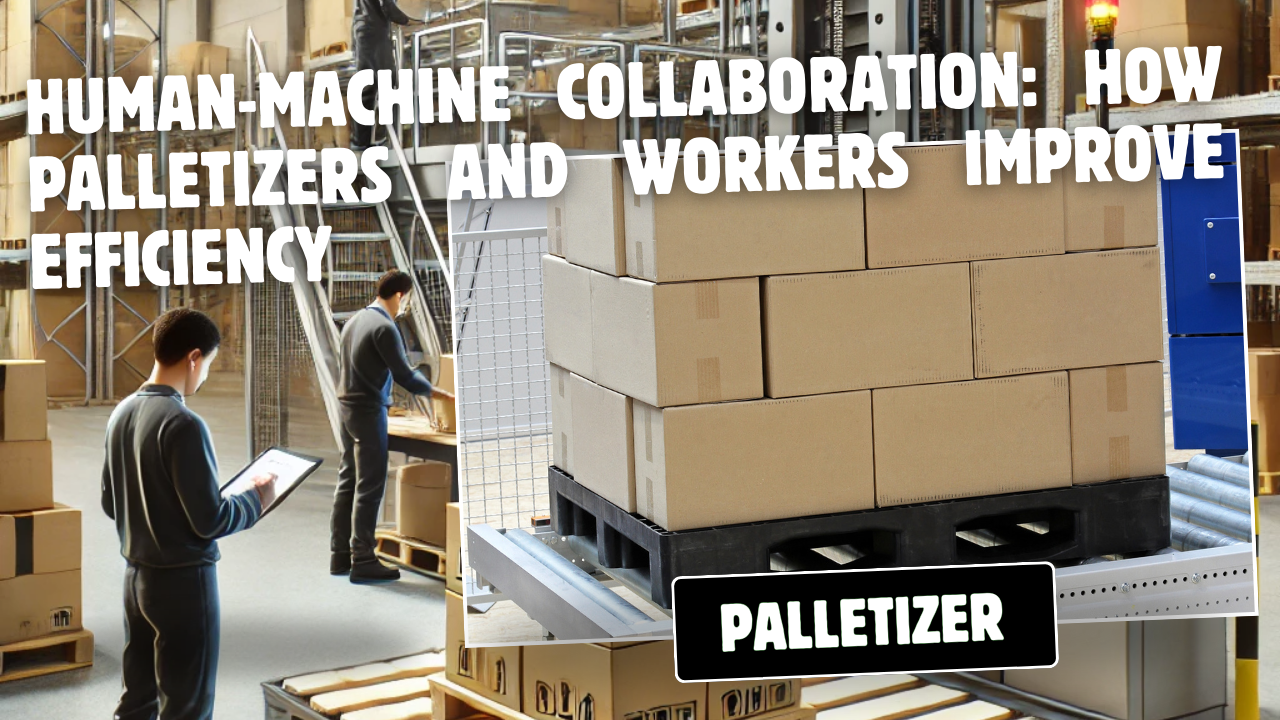
Human-Machine Collaboration: How Palletizers and Workers Improve Efficiency
With the rise of automation, palletizers are increasingly used in logistics, manufacturing, and warehousing. While automation boosts productivity and reduces manual labor, human workers still play an essential role.
Human-machine collaboration combines the strengths of both to create more efficient and flexible workflows. This article explores how palletizers and workers collaborate and how optimized workflows can enhance overall efficiency.
1. Division of Labor Between Palletizers and Workers
Palletizers handle repetitive tasks such as lifting, stacking, and moving products. Workers focus on tasks that require flexibility and decision-making, such as quality control, machine maintenance, and handling exceptions. This division allows machines to work quickly and precisely, while humans address more complex challenges. For instance, in a packaging facility, a palletizer stacks boxes while workers monitor quality and resolve issues, boosting overall efficiency.
2. Safety in Collaboration
Safety is a top priority in human-machine collaboration. Modern palletizers are equipped with sensors that detect the presence of workers and adjust their operations accordingly, such as slowing down or pausing to prevent accidents. Barriers or virtual safety zones ensure that human operators can work near machines without risk, creating a safer and more productive environment.
3. Evolving Worker Roles
As automation advances, worker roles shift. Rather than performing manual labor, workers now oversee machines, troubleshoot, and adjust settings as needed. Workers interact with palletizers through user-friendly interfaces like touchscreens and tablets, enhancing their technical skills and reducing physical strain. This collaborative approach empowers workers to manage more complex tasks while reducing their manual workload.
4. Optimizing Workflow
Optimized workflows can further improve the efficiency of palletizers and workers. For example:
Real-time data and feedback: IoT technology can provide live data from palletizers, allowing workers to make quick adjustments.
Flexible task allocation: Automated systems can adapt to changes in production demands, speeding up palletizers when needed while reallocating workers to maintenance or quality control.
Preventive maintenance: Using data analytics and machine learning, palletizers can predict potential breakdowns, enabling workers to perform maintenance in advance, reducing downtime.
5. Increased Flexibility on the Production Line
Human-machine collaboration increases flexibility. In traditional fully automated lines, changes in product design or custom orders can require reprogramming, leading to downtime. However, with human oversight, workers can make quick adjustments during production, enabling businesses to respond to custom orders or changes without stopping the line.
6. Training and Skill Development
Workers need to be trained to operate and maintain palletizers, which enhances their skill set and prepares them for more advanced roles. Companies can invest in training programs, online courses, and hands-on experience, enabling workers to adapt to new technologies while improving job satisfaction and reducing turnover.
7. Economic Benefits of Human-Machine Collaboration
The economic impact of human-machine collaboration is significant. Palletizers handle time-consuming, repetitive tasks, allowing workers to focus on high-value activities. This leads to lower labor costs, fewer errors, and higher production quality. The increased efficiency also reduces production times and speeds up product delivery, giving businesses a competitive edge.