The importance of safety signs in case erector
2025-04-09
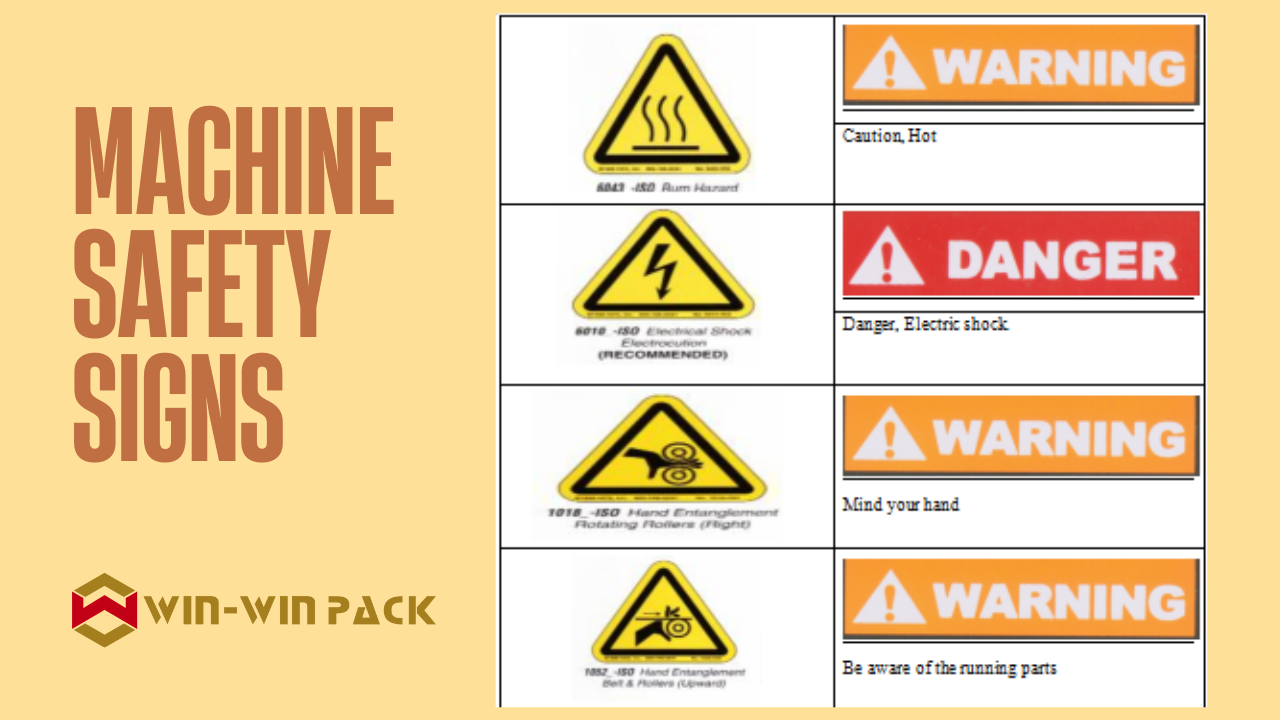
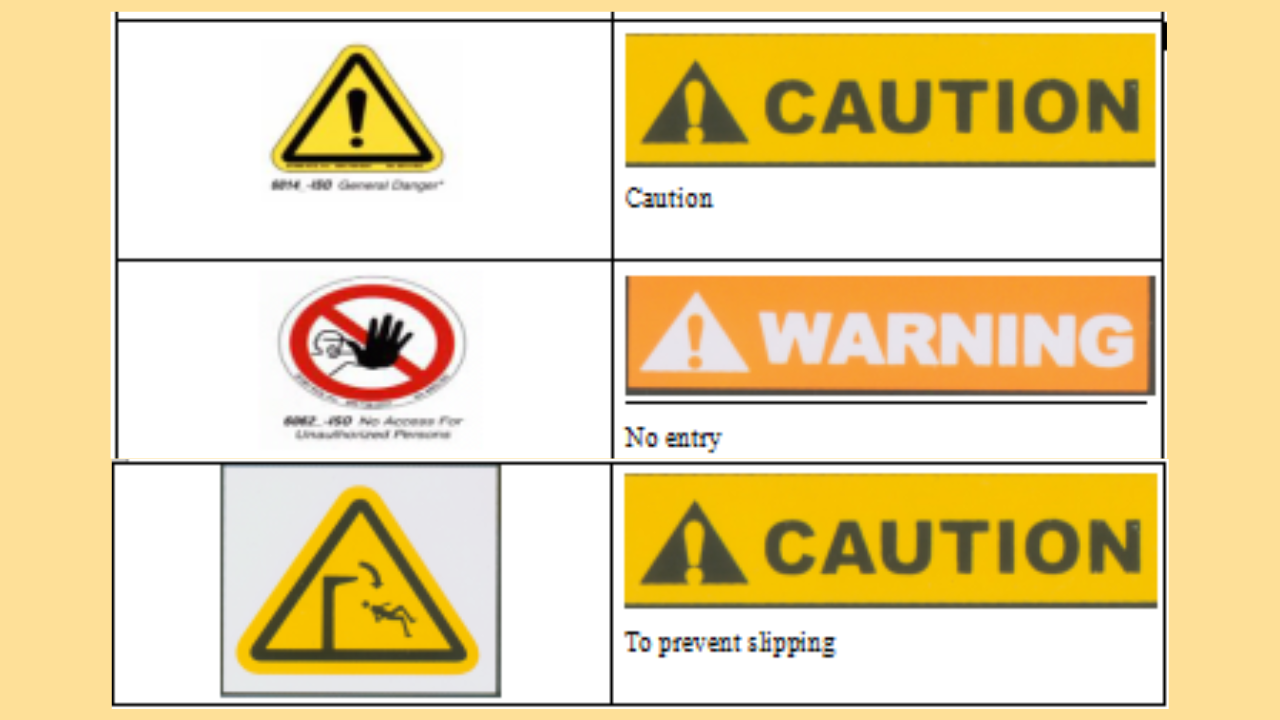
The Importance of Safety Signage in Case Erector: A Professional Overview
Case erectors are essential components in modern packaging lines, widely used across industries including food, pharmaceuticals, and logistics. While these machines significantly enhance operational efficiency by automating the carton erecting process, they also introduce various mechanical and electrical risks. To mitigate these hazards, the implementation of standardized safety signage and operator safety training is critical to maintaining a safe production environment.
Key Types of Safety Signage and Their Functions
Identifies components or areas with elevated temperatures, such as sealing heads or electrical enclosures. Operators must avoid direct contact to prevent thermal burns.
Highlights areas with potential electrical danger, particularly during maintenance of control panels or wiring systems. Proper lockout/tagout (LOTO) procedures are essential.
Alerts to pinch or crush points, especially near conveyors, pneumatic actuators, or carton folding mechanisms. These areas pose a high risk for hand injuries.
Marks moving components like shafts or belts, warning operators to avoid entanglement with clothing, gloves, or body parts.
Serves as a catch-all alert for non-specific risks. It reminds operators to proceed with caution in various machine zones.
Indicates zones limited to authorized personnel only, such as inside electrical cabinets or behind safety guards.
Identifies areas where liquid or dust accumulation may cause slips, helping to prevent fall-related injuries.
Core Safety Measures for Operating Case Erector
Operators should consistently wear appropriate PPE including safety gloves, eyewear, and protective footwear, based on the specific risks identified in the machine's risk assessment.
Preventive maintenance ensures optimal machine performance and early detection of mechanical or electrical faults. All maintenance should be documented and performed by trained personnel.
Operators must be trained to follow standardized operating protocols outlined in the machine manual. Unauthorized parameter adjustments or bypassing safety interlocks can result in severe injury.
Machines should be equipped with clearly marked and easily accessible emergency stop buttons and interlock systems that halt operation immediately during unsafe conditions.
Prior to operating case erectors, personnel must undergo training covering machine function, risk awareness, troubleshooting, and emergency procedures. Continuous safety education reinforces best practices.
Safety signage serves not only as a regulatory requirement but also as a frontline defense against accidents in high-speed automated environments. In case erectors, where multiple mechanical systems operate in coordination, clearly displayed and internationally recognizable safety signs are critical for protecting personnel.
Manufacturers must take a proactive approach by combining proper signage, equipment design, operator training, and routine inspections. A well-executed safety strategy not only minimizes downtime due to accidents but also builds a safety-first culture that ensures both productivity and compliance in modern packaging operations.